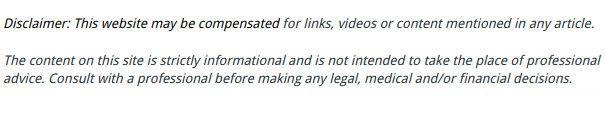
In the world of manufacturing, design is a critical component that impacts efficiency, productivity, and success. Let’s explore key considerations across equipment, office, and business elements to optimize design for manufacturing companies. Through proper design implementation, companies can enhance their operations and drive competitive advantage.
Manufacturing Equipment Selection
The selection of manufacturing equipment plays a crucial role in ensuring production efficiency. Companies need to conduct thorough research and benchmarking for optimal equipment that aligns with their production requirements and budget constraints. Partnering with a reputable natural gas odorant supplier can aid in maintaining equipment by ensuring that systems relying on natural gas operate effectively and safely.
Technological advancements have significantly influenced the types of machinery available to manufacturers today. Factories can leverage robotics, AI, and IoT-enabled devices to enhance precision and reduce manual labor. It’s vital to remain updated with the latest trends to identify solutions that promise productivity gains.
Maintaining the machinery through regular maintenance and periodic upgrades is also a key consideration. Employing advanced adhesive solutions in equipment assembly can prevent frequent breakdowns and enhance durability. Reducing downtime through effective maintenance strategies fosters productivity and aligns with objectives.
Facility Layout and Design
The layout of a manufacturing facility greatly impacts the flow of operations and overall efficiency. Strategic facility design means prioritizing equipment placement for reduced transit time and minimal disruption. Through effective load testing, facilities can ascertain and optimize the support structure to accommodate large and heavy machinery, seamlessly aligning with goals.
A well-thought-out facility layout incorporates areas for raw material storage, production, quality control, and finished goods storage. Organizing these spaces within a facility minimizes material handling efforts and ensures streamlined processes, ultimately enhancing manufacturing efficiency. Implementing flexible layouts can also adapt to changes in demand or production processes. Modular designs allow for easy alterations and quick adaptation to dynamic market needs, supporting scalability. This adaptability aids in maintaining effectiveness for design for manufacturing companies while responding to shifting manufacturing landscapes.
Lean Manufacturing Implementation
Lean manufacturing principles are essential in reducing waste and increasing value in manufacturing processes. The implementation of lean methodologies focuses on improving quality, cost, delivery, and performance, often leading to significant competitive advantages. Manufacturing companies aiming for a level of efficiency frequently adopt practices such as just-in-time inventory and continuous improvement.
Incorporating lean principles demands a thorough understanding of current manufacturing processes and identifying key areas for improvement. This approach enhances the precision of production forecasts and optimizes resource utilization. Aiming for sustained growth requires aligning strategies with lean manufacturing initiatives.
Companies investing in lean manufacturing can benefit from reduced operational costs, increased flexibility, and improved employee morale. Creating a culture that embraces continuous improvement encourages employees to identify solutions that drive operational excellence. Design for manufacturing companies becomes a natural outcome of adherence to these lean principles and practices.
Material Handling Systems
Material handling systems are essential in improving the efficiency of moving, protecting, storing, and controlling materials. Effective systems minimize product damage, lower costs, and improve quality, profitability, and productivity. A core aspect of achieving targets is optimizing these systems, utilizing tools like a colony counter to ensure accuracy in inventory counts.
To maximize efficiencies, flexibility in material handling systems should be taken into account to adapt to changing production dynamics. Technology-driven solutions such as automated guided vehicles (AGVs) or conveyor systems are being increasingly integrated to complement manual material handling efforts. Ensuring a robust framework aligns with company-wide objectives.
Safety is a primary concern in material handling, necessitating the implementation of effective training programs for employees. Well-designed material handling processes reduce the likelihood of accidents and enhance overall safety in the workplace. Such adherence to safety protocols aligns with the company’s comprehensive strategy.
Energy Efficiency Measures
Energy efficiency is a crucial consideration for manufacturing companies aiming to reduce operational costs and their carbon footprint. Implementing energy-efficient technologies and practices can significantly cut energy consumption. Manufacturing companies regularly incorporate initiatives by leveraging energy audits to identify areas for improvement in their operations.
Solutions such as installing energy-efficient lighting, optimizing HVAC systems, and using high-efficiency commercial electric water heaters contribute to substantial savings. Investing in renewable energy sources further boosts sustainability contributions, resulting in long-term benefits and environmental stewardship.
Energy efficiency isn’t limited to equipment but expands to encompass production processes. Evaluating heat recovery systems, compressed air systems, and waste reduction strategies can yield additional improvements. Incorporating these elements is a step toward achieving optimal outcomes for environmentally conscious manufacturing facilities.
Office Space Planning
Thoughtful office space planning is vital for enhancing productivity and employee satisfaction when it comes to design for manufacturing companies. An office that complements manufacturing operations fosters seamless communication between departments. Engaging professional office construction services ensures the creation of spaces that fulfill functional needs while supporting initiatives for a cohesive work environment.
Flexible office layouts that incorporate breakout zones, collaborative spaces, and technology enhancements can propel productivity. These spaces are designed to encourage teamwork, innovation, and idea-sharing. Aligning office design with goals helps in achieving a balance between aesthetic appeal and practical functionality.
Office environments should also focus on ergonomics and adaptability to support employee well-being. Scalability and layout flexibility will accommodate future expansion or modifications as business needs evolve. By prioritizing these elements, manufacturing companies can ensure that office spaces align with their overarching objectives.
Technology and Automation Integration
The integration of technology and automation is pivotal to optimizing manufacturing processes. Advanced technologies expedite production tasks, reduce errors, and lead to innovative solutions, aligning with the broader goals. As part of this consideration, employing systems like medical device inventory management software enables seamless tracking and control over inventory.
Automation technology can range from robotic arms on the production line to computer-aided manufacturing tools. Integrating these technologies provides real-time data for improved decision-making and enhances process efficiency. This alignment with standards ensures that manufacturing companies maintain their competitive edge.
However, integrating new technologies should be met with a structured approach, ensuring technological compatibility and employee readiness. Continuous training and development are necessary to leverage new systems effectively. Embracing these initiatives as part of a company’s core strategy ensures a future-ready manufacturing operation.
Employee Training and Safety Programs
Employee training and comprehensive safety programs are imperative for maintaining high productivity and minimizing workplace hazards. These initiatives form a critical part of any strategy aiming to support a safe and knowledgeable workforce. Ensuring access to certified training enhances employee skills, enabling them to adapt to evolving manufacturing techniques.
Safety programs should encompass all aspects of manufacturing operations, incorporating protocols for material handling, machinery operation, and emergency procedures. Establishing partnerships with commercial cleaning services can further contribute to maintaining a clean and hazard-free environment. Adhering to rigorous standards reinforces a company’s overarching objectives for design for manufacturing companies.
Regularly reviewing and updating training programs ensures they keep pace with technological advancements and regulatory changes. This proactive approach enhances safety culture while minimizing the potential for accidents. Through continued investment in training and safety, companies underscore their commitment to comprehensive strategies.
Compliance with Industry Standards
Compliance with industry standards is non-negotiable for manufacturing companies striving to maintain quality, safety, and market competitiveness. Adhering to regulatory requirements and industry certifications ensures that products meet customer expectations and legal benchmarks. Companies focusing on initiatives regularly review their processes against industry norms to ensure compliance.
Engaging in compliance audits and embracing advanced adhesive solutions can solidify manufacturing quality and product performance. Understanding standard rules and procedures ensures seamless operations and minimizes disruptions. Aligning compliance efforts with business objectives reinforces a company’s strategic framework.
Continuous monitoring and participation in industry groups help manufacturing companies remain updated on regulatory changes. This forethought ensures compliance and allows manufacturers to anticipate shifts that may impact future operations. Incorporating these standards is essential for sustaining a company’s commitment to its manufacturing practices.
Maintenance and Repair Strategies
Comprehensive maintenance and repair strategies are fundamental to extending equipment lifespan and reducing downtime in manufacturing environments. Implementing a proactive maintenance schedule helps in identifying potential issues before they evolve into significant problems. Companies keen on achieving goals must adopt systematic maintenance approaches.
Leveraging technology in maintenance, such as predictive analytics and IoT-enabled monitoring systems, can revolutionize how maintenance tasks are managed. Such integration enables timely interventions, thereby maintaining optimal operation levels and enhancing efficiency in production workflows.
Effective rust removal techniques, along with regular inspections, are vital for maintaining equipment integrity and performance. These measures protect valuable assets from decay and preserve productivity over time. Maintenance strategies forming part of a company’s agendas contribute to sustained quality outputs.
Supply Chain and Inventory Management
Efficient supply chain and inventory management are integral for design for manufacturing companies to meet production demands and manage costs effectively. Leveraging advanced logistics solutions and inventory management best practices can optimize stock levels, reduce wastage, and enhance resource utilization. Embedding principles in these processes fosters a responsive and agile supply chain.
The utilization of medical device inventory management software strengthens the capability to track inventory accurately and in real time. This technological adoption prevents overstocking, ensures high stock turnover, and minimizes capital tied in inventory. These strategies align with principles, supporting streamlined operations.
Collaboration with suppliers and implementation of just-in-time procurement can further fortify supply chain efficiency. These partnerships foster transparency and build trust, facilitating smoother transitions and deliveries. Integrating these principles as part of a company’s strategy ensures competitive advantage and operational excellence.
Sustainable Manufacturing Practices
Sustainable manufacturing practices are becoming essential in today’s environmentally conscious world. Companies are increasingly integrating eco-friendly solutions, such as process optimizations and greener supply chain practices, aligning with sustainability initiatives. Emphasizing sustainability not only helps in resource conservation but also meets customer expectations and regulatory demands.
Incorporating technologies such as energy-efficient commercial electric water heaters and sustainable waste management can drastically reduce a company’s environmental footprint. Optimizing material usage and minimizing waste generation are core aspects of implementing sustainable practices. These efforts contribute to achieving a standard of sustainable operations.
Manufacturers aiming to enhance sustainability are investing in renewable energy and energy-efficient practices. Leveraging solar panels, wind energy, or other renewable sources can be instrumental in reducing reliance on non-renewable energy. Through these initiatives, companies fulfill their commitments while driving positive environmental impacts.
Customer-Focused Product Design
Customer-focused product design is instrumental in gaining a competitive edge and ensuring product success. Manufacturing companies must focus on understanding customer needs and preferences as part of their design strategy. Integrating customer feedback into the product development cycle bolsters a company’s adherence to its objectives.
Leveraging market research and data analytics allows manufacturers to tailor their designs to meet specific market demands. This adaptable approach ensures that products are not only functional but also resonate with end-users. A commitment to customer-centric design reflects a focus on innovation and market alignment and helps determine design for manufacturing companies.
Collaboration between teams and customer representatives can facilitate the development of products that address real-world challenges and preferences. Creating a feedback loop that incorporates user experiences heightens product success and acceptance. These strategies embody a company’s broader approach centered around customer satisfaction and loyalty.
IT and Communication Infrastructure
Robust IT and communication infrastructure is a linchpin for efficient design for manufacturing companies. Establishing and maintaining a reliable communication network ensures seamless information flow throughout the organization. This infrastructure supports the broader objectives, enabling swift decision-making and collaboration across departments.
Investing in cloud computing and data analytics offers companies the ability to store, analyze, and leverage vast amounts of information. This capability provides insights into production trends, streamlining processes and enhancing productivity. By committing to digital transformation, manufacturers reinforce their focus on operational excellence.
Cybersecurity is another critical component of IT infrastructure, ensuring the protection of sensitive data against threats. Regularly updating and maintaining security protocols is vital to safeguarding company assets and operations. Aligning IT investments with the company’s strategies allows for sustainable and secure business operations.
Branding and Marketing Strategy
Effective branding and marketing strategies are essential for manufacturing companies to reach and engage their target audience. Developing a strong brand identity helps differentiate a company in a competitive market and fosters customer loyalty. Crafting a marketing strategy that includes platforms like website design can increase visibility and market presence.
Digital marketing campaigns, SEO optimization, and social media engagement are pivotal components of modern marketing efforts. These strategies help communicate brand values and product offerings to a wider audience. By investing in cohesive branding, companies reaffirm their dedication to achieving standards in marketing excellence.
Engaging storytelling over multiple channels can humanize a brand and build a lasting connection with customers. Consistent messaging and visual elements strengthen brand recognition and trust. Enshrining these principles within a company’s blueprint secures sustained customer engagement and market success.
Financial Planning and Budgeting
Financial planning and budgeting are foundational to managing operations and ensuring the long-term success of manufacturing companies. Crafting realistic budgets that account for potential variables provides foresight into future financial states. By aligning these practices with goals, companies ensure preparedness and strategic resource allocation.
Regular financial analysis and forecasting equip companies with insights into cash flow, potential investments, and economic challenges. These evaluations facilitate informed decision-making, stability, and growth. Embarking on strategic financial planning aligns with aspirations for sustainable, efficient operations.
Managing fiscal health involves balancing operational costs, capital investments, and potential risks. By anticipating financial contingencies, companies reinforce their resilience against economic uncertainties. Integrating these strategies into the company’s focus underscores its long-term viability and exploratory growth.
These elements of design for manufacturing companies in terms of equipment, offices, and business are integral to modern manufacturing companies’ success. By understanding and implementing these key considerations, businesses can enhance efficiency, adaptability, and competitiveness in today’s dynamic market. Companies embracing these strategies are more likely to secure sustained operational success and industry leadership.